
Cybord uses smart tech to test, analyze, and track components, speeding up work and reducing errors.

AOI - (Automated Optical Inspection)
The Problem
The user filters data and exports it to Excel, spending at least 3-5 hours finding faulty components. This process is time-consuming and inefficient.

Excel limitations:
Excel filters are limited in handling complex date ranges, requiring manual updates and lacking automation for repetitive or larger tasks.
The Challenges
-
Users expect continuity; changes to the component page can disrupt their expectations.
-
Users are highly familiar with the current table design, having used it for years.
-
Changing the table design may disrupt established user habits and workflows, leading to confusion and inefficiency.
Persona

User Interview- Conclusions
After talking with the user, I gained insights that need improvement:
-
Filter Accessibility: The filter is not prominently placed, making it less accessible to the user.
-
Excel File Testing: testing components in excel takes at least 3-5 hours.
Balancing Business Goals and User Needs
-
Achieving at least a 60% reduction in file processing time, lowering it from 180 minutes (3 hours) to less than 30 minutes per session.
-
Improving user experience, expanding our customer base by 10%, and maintain high retention rates.
Mid fidelity wireframe
-
After researching complex systems and consulting the team, I suggest to keep the table display with an integrated filter, as the filter is primary for accessibility.
​
-
In collaboration with the product manager and development manager, we considered grouping the components to save time working on the file.
The table view (second version)
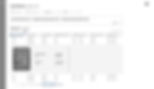
Solution
Filter components groups by minimum quantity- e.g: 2,000
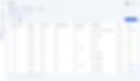.jpg)
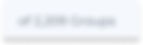

Export a prepared file with the component groups.
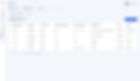
The final version- prod
Users now have the capability to filter data by groups of components before downloading it to a file, as seen in the first column.
Outcome
-
We have successfully reduced the time from 3 hours to less then (30 minutes), achieving an 83.33% reduction in time.
-
The process optimization has brought a 60% improvement in efficiency for users in identifying defective components.
-
There is a significant improvement in retaining existing customers and expanding the customer base by 15%, but further improvements are required.
Conclusions
The project began with an interview with a key customer to gather feedback and improve user experience within budget and time constraints. While progress was made, there’s still room for deeper research, and it's important to incorporate more professional research tools moving forward.
Thanks to the team for their collaboration and support throughout this process!